Phenolic resins are mainly used in the manufacture of various plastics, paints, adhesives and synthetic fibres.
Release time:
2024-06-20
Phenolic resins are mainly used in the manufacture of various plastics, paints, adhesives and synthetic fibres.
Compression moulding powder
One of the main uses of phenolic resins is the production of compression moulding powder for moulded products. Using roller pressing method, screw extrusion method and emulsion method to make the resin impregnated with fillers and other additives mixed evenly, and then crushed and sifted can be made to pressure moulding powder. Commonly used wood powder as filler, for the manufacture of certain high electrical insulation and heat-resistant parts, but also with mica powder, asbestos powder, quartz powder and other inorganic fillers. Compression moulding powder can be made into various plastic products by moulding, transfer moulding and injection moulding. Thermoplastic phenolic resin compression moulding powder is mainly used in the manufacture of switches, sockets, plugs and other electrical parts, daily necessities and other industrial products. Thermosetting phenolic resin compression moulding powder is mainly used for manufacturing high electrical insulation parts. Reinforced phenolic plastics to phenolic resin (mainly thermosetting phenolic resin) solution or emulsion impregnated with various fibres and fabrics, by drying, pressing and moulding of a variety of reinforced plastics is an important industrial material. It is not only high mechanical strength, good overall performance, and can be mechanically processed. Glass fibre, quartz fibre and its fabric reinforced phenolic plastics are mainly used in the manufacture of various brake friction plates and chemical anti-corrosion plastics; high silica glass fibre and carbon fibre reinforced phenolic plastics is an important aerospace industry ablation-resistant materials.
Phenolic coatings Phenolic resins modified with rosin, butanol etherified phenolic resins, as well as p-tert-butyl phenolic resins, p-phenyl phenolic resins and tung oil, linseed oil have a good miscibility, is an important raw material for the paint industry. The first two are used to formulate low and medium grade paints, and the latter two are used to formulate high grade paints.
Phenolic Resin
Thermosetting phenolic resin is also an important raw material for adhesives. Single phenolic resin adhesive brittle, mainly used for plywood and fine casting sand bonding. Adhesives based on other polymer-modified phenolic resins occupy an important position in structural adhesives. Among them, phenolic - nitrile, phenolic - acetal, phenolic - epoxy, phenolic - epoxy - acetal, phenolic - nylon and other adhesives are characterised by good heat resistance and high bond strength. Phenolic - nitrile and phenolic - acetal adhesive also has tensile, impact resistance, moisture and heat aging resistance and other excellent properties, is an excellent variety of structural adhesives.
Phenolic Fibre
Mainly thermoplastic linear phenolic resin as raw material, after melt spinning immersed in aqueous solution of paraformaldehyde and hydrochloric acid for curing, to get the formaldehyde crosslinked body structure fibre. In order to improve the strength and modulus of the fibre, it can be melt blended with 5% to 10% polyamide and then spun. This kind of fibre is golden or yellow-brown fibre, strength of 11.5 ~ 15.9cN/dtex, outstanding flame-resistant performance, the ultimate oxygen index of 34, instantaneous contact with nearly 7500 ℃ oxygen - acetylene flame, does not melt or delayed combustion, with self-extinguishing, but also resistant to concentrated hydrochloric acid and hydrofluoric acid, but resistant to sulphuric acid, nitric acid and alkali performance is poor. It is mainly used as protective clothing and flame-resistant fabrics or interior decorations, and can also be used as insulation, heat insulation and adiabatic, filtration materials, etc. It can also be processed into low-strength, low-modulus carbon fibre, activated carbon fibre and ion exchange fibre.
Anti-corrosion materials
Thermosetting phenolic resin is commonly used in the field of corrosion prevention in several forms: phenolic resin coatings; phenolic resin FRP, phenolic - epoxy resin composite FRP; phenolic resin mastic, mortar; phenolic resin impregnation, pressed graphite products. The curing form of thermosetting phenolic resin is divided into room temperature curing and heat curing. Room temperature curing can use non-toxic room temperature curing agent NL, can also use benzene sulfonyl chloride or petroleum sulfonic acid, but the latter two materials are more toxic, irritating. It is recommended to use low toxicity and high efficiency NL curing agent. Filler can choose graphite powder, porcelain powder, quartz powder, barium sulphate powder, not suitable for pyrophyllite powder.
Thermal insulation and heat preservation material
Mainly phenolic resin foaming material, phenolic foam products are characterized by thermal insulation, heat insulation, fire prevention, lightweight, as insulation, energy saving, fire prevention of new materials can be widely used in central air-conditioning systems, lightweight thermal insulation of colour steel panels, housing insulation and energy reduction of heat preservation, chemical pipeline insulation materials (especially deep low temperature insulation), cars and ships, and other places in the field of heat preservation. Phenolic foam is known as the king of thermal insulation because of its low thermal conductivity and good thermal insulation performance. Phenolic foam not only low thermal conductivity, good thermal insulation performance, but also has flame retardant, good thermal stability, light weight, low smoke, low toxicity, heat resistance, high mechanical strength, sound insulation, strong chemical corrosion resistance, marble type good, etc. A number of advantages, phenolic foam raw materials from a variety of sources, the price is low, and production and processing is simple, the product has a wide range of uses.
NEWS
Furan resins are thermosetting resins that cross-link with each other when heated and cure without the addition of a hardener. Acids play a catalytic role in the curing reaction and also reduce the temperature required for heat curing.
One of the main uses of phenolic resins is the production of compression moulding powder for moulded products. Using roller pressing method, screw extrusion method and emulsion method to make the resin impregnated with fillers and other additives mixed evenly, and then crushed and sifted can be made to pressure moulding powder.
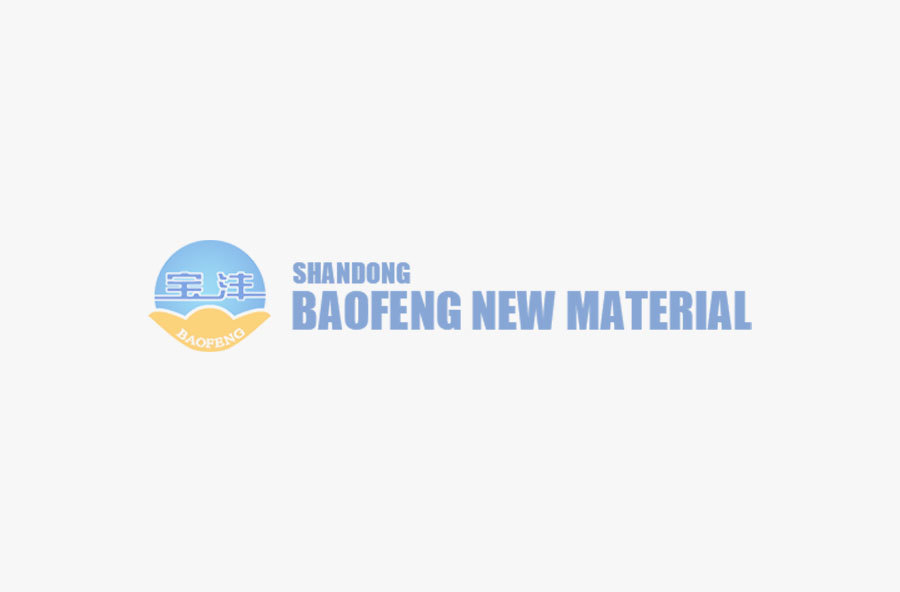
The solid phenolic resin is a yellow, transparent, amorphous mass.
Solid phenolic resin is yellow, transparent, amorphous lumpy substance, slightly reddish due to free phenol, the specific gravity of the entity is about 1.7 on average, easily soluble in alcohol, insoluble in water, stable to water, weak acid, weak alkali solution.
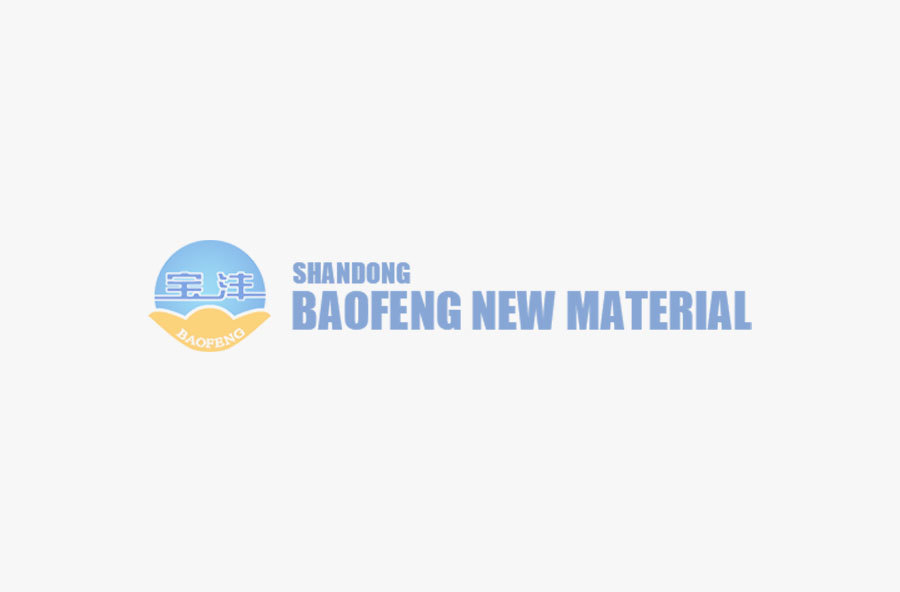
New phenolic resin can be used as a bonding agent for diamond grinding wheels
New phenolic resin can be used as a bonding agent for diamond grinding wheels, the use of new phenolic resin and phenolic resin mixed with 1:3, not only improves the strength of phenolic resin, but also improves the heat resistance and grinding ratio. If the new phenolic resin is used alone,
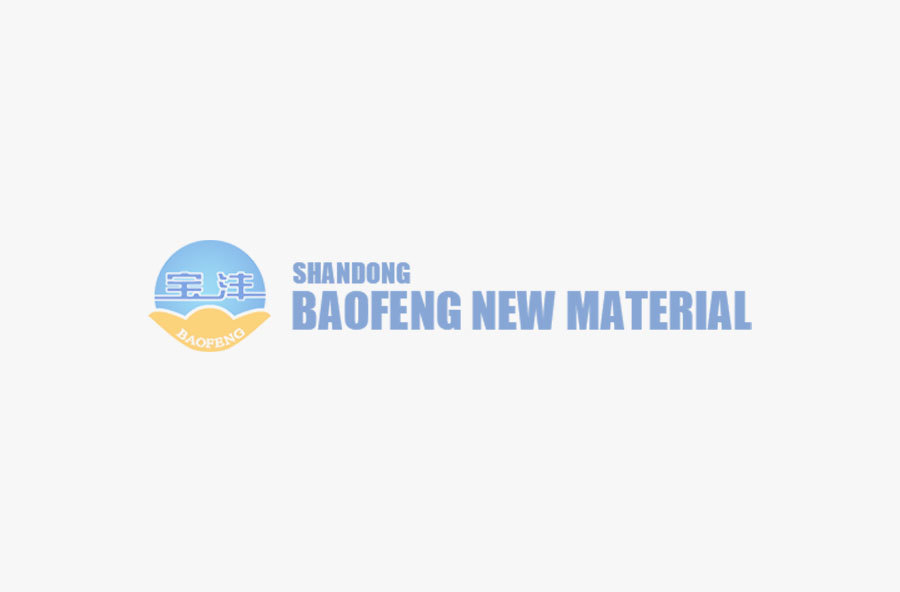
New phenolic resins are polymer compounds
New Phenolic Resin is a polymer compound, which is produced by the condensation reaction between phenol and aryl ether. New phenolic resin has good mechanical properties, heat resistance, widely used in diamond products
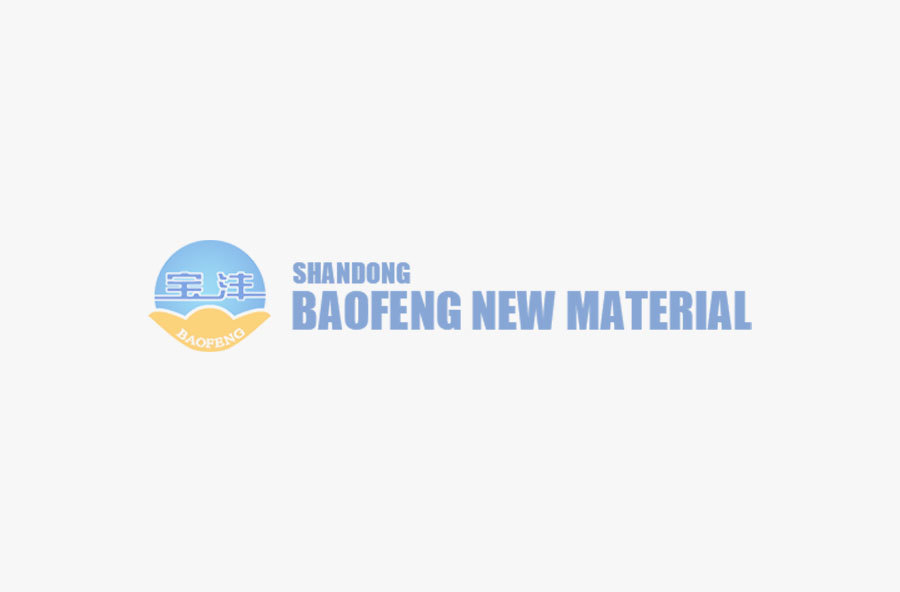
Furan Resin Properties and Applications
Properties and applications of furan resins--Uncured furan resins have good mixing properties with many thermoplastic and thermosetting resins, so they can be modified by mixing with epoxy resins or phenolic resins.